Aluminum bottoms, often used in cookware, offer several advantages:
- Heat Conduction: Aluminum is an excellent conductor of heat, distributing it evenly across the surface of the cookware. This ensures that food cooks uniformly without hot spots, reducing the chances of burning or uneven cooking.
- Lightweight: Aluminum is lightweight compared to many other metals used in cookware. This makes handling easier, especially for larger pots and pans.
- Cost-effective: Aluminum is relatively inexpensive compared to other metals like copper or stainless steel, making aluminum-bottomed cookware more affordable while still providing good heat distribution.
- Durability: While aluminum can dent or scratch more easily than some other metals, when used as a bottom layer in cookware alongside other materials (like stainless steel or anodized aluminum), it enhances the durability of the cookware.
- Compatibility: Aluminum bottoms are often used in combination with other materials in cookware, such as stainless steel or copper. This combination capitalizes on the strengths of both materials, creating a more versatile and efficient cooking experience.
- Energy Efficiency: Due to its excellent heat conduction, aluminum bottoms can potentially reduce cooking time and energy consumption since they heat up quickly and evenly.
Remember, while aluminum bottoms have their advantages, pure aluminum cookware might react with certain acidic foods, altering taste and appearance. That’s why many aluminum-bottomed cookware sets feature protective layers or coatings to prevent this interaction and maintain food quality.
Aluminum bottoms offer several advantages when used in various products, including cookware, electronics, and more:
- Heat Conductivity: Aluminum is an exceptional conductor of heat. When used as a bottom layer in cookware, it ensures even distribution of heat throughout the cooking surface. This helps in preventing hot spots and allows for uniform cooking.
- Lightweight: Aluminum is relatively lightweight compared to other metals like stainless steel or copper. This property makes products with aluminum bottoms easier to handle and maneuver.
- Cost-Effectiveness: Aluminum is more affordable than many other metals used in manufacturing. Incorporating aluminum into the bottom layer of products helps keep production costs down, making the final product more economical for consumers.
- Energy Efficiency: Due to its excellent heat conductivity, aluminum bottoms heat up quickly and evenly. This property can reduce cooking times and energy consumption, making it an energy-efficient choice for cookware.
- Durability: While pure aluminum can be relatively soft and prone to dents or scratches, aluminum bottoms are often combined with other materials like stainless steel or coated for added durability and strength.
- Versatility: Aluminum’s compatibility with various coatings and treatments makes it versatile for use in different products. For instance, in electronics, an aluminum bottom can aid in heat dissipation, preventing overheating.
- Corrosion Resistance: Aluminum has a natural resistance to corrosion, making it suitable for use in environments where exposure to moisture or certain chemicals is a concern.
- Recyclability: Aluminum is highly recyclable, allowing for the production of environmentally friendly products. Recycling aluminum requires significantly less energy compared to producing new aluminum, making it a sustainable material choice.
While aluminum bottoms offer numerous advantages, it’s important to note that in certain applications, pure aluminum might not be the best choice due to its reactivity with certain substances. Hence, it’s often used as part of composite materials or treated to prevent adverse reactions.
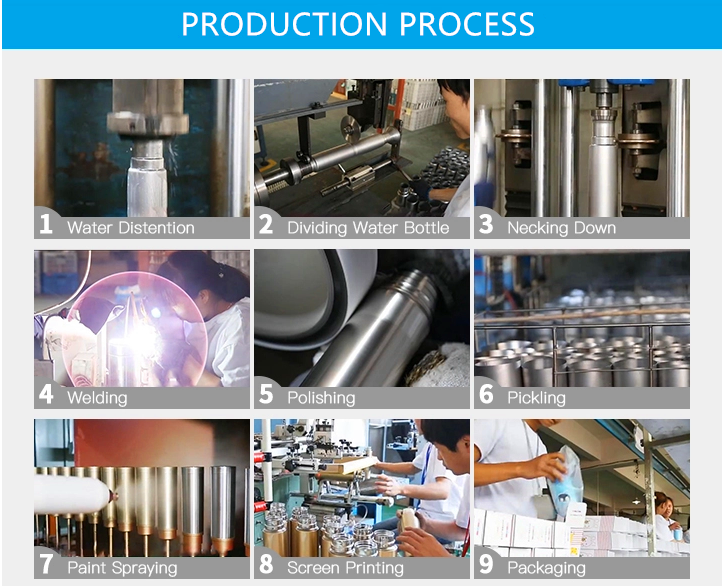
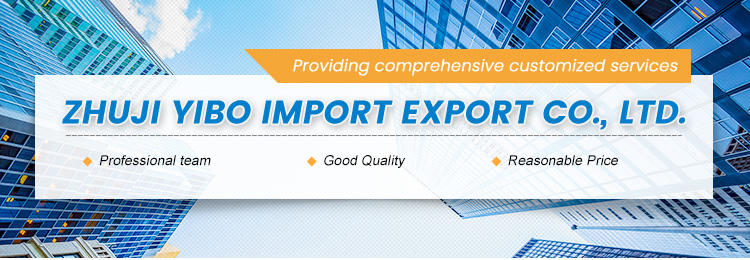